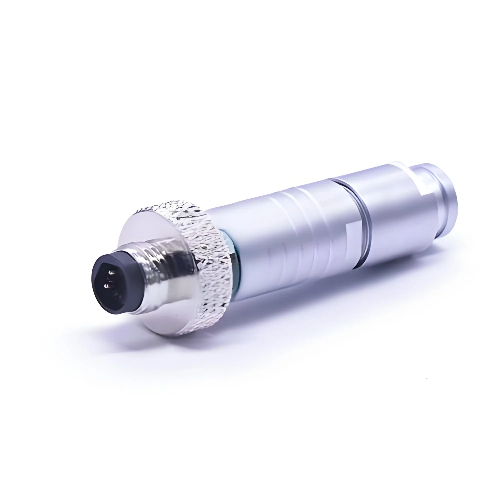
The Evolution of Circular Connectors: From Legacy Systems to Modern Solutions
Are you tired of dealing with unreliable connections in harsh environments? Your industrial systems cut out at the worst times. Your equipment fails when exposed to moisture. Your connectors just can’t keep up with today’s data demands. At YW Connectors, we understand these frustrations and have the solutions you need.
The Problem: Legacy Circular Connectors Can’t Meet Today’s Demands
Old circular connectors are holding back your operations. They were good once, but now:
- They are too bulky for modern compact designs
- They have high contact resistance causing signal loss
- They offer limited EMI shielding against interference
- They fail in harsh environments due to vibration and corrosion
- They can’t handle the high-speed data your operations need
These outdated systems aren’t just inconvenient – they’re costing you money through downtime, repairs, and lost productivity.
The Pain Gets Worse
This problem isn’t going away on its own. In fact:
- 35% of industries report compatibility issues when mixing legacy and modern connector systems
- Retrofitting legacy connectors for digital systems cost the U.S. Navy $1.2 million in just one project
- Legacy connectors are 2x more likely to fail in high-vibration environments
- With Industry 4.0 and IoT adoption growing, the gap between what your old connectors can do and what you need them to do is getting wider every day
Without a proper solution, you risk falling behind competitors who are upgrading to modern connectivity solutions.
The Solution: YW’s Advanced Circular Connector Systems
YW Connectors is a leading electrical connector manufacturer with solutions that solve these problems. Our modern circular connectors offer:
- Advanced Materials & Manufacturing
- Thermoplastic shells that reduce weight by up to 40%
- Gold-plated contacts that reduce resistance by 50% compared to tin
- Modular designs for easy customization and field maintenance
- Smart & IoT-Ready Connections
- IoT-enabled sensors in select models
- Hybrid power+data transmission in a single connector
- Up to 10 Gbps data rates for 5G-ready applications
- Industry-Specific Innovations
- Waterproof circular connectors with IP67/IP68 ratings
- Industrial circular connectors for manufacturing
- Metal circular connectors for extreme durability

The Historical Context: How We Got Here
Circular connectors have come a long way since their early days. Here’s a quick look at their evolution:
Early Designs & Standards (1940s-1970s)
- MIL-DTL-5015 and DIN connectors emerged after World War II
- Made with aluminum shells and solder cup terminations
- Primarily used in military equipment and heavy machinery
- Bulky designs focused on mechanical strength over efficiency
The Transition Period (1980s-2000s)
- Miniaturization demands drove smaller connector designs
- The digital revolution created need for high-speed data transmission
- Stricter industry standards emerged for waterproofing (IP67/IP68)
- MIL-STD-348 set new benchmarks for reliability
Today’s Modern Solutions (2000s-Present)
- Smart connectors with embedded sensors are now the standard
- The global circular connector market will reach $2.8 billion by 2027
- 85% of industrial robots now use advanced M12/M8 connectors
- Modern connectors last 3x longer than legacy models
Real-World Applications Across Industries
Our modern circular connectors are making a difference in:
Defense & Aerospace
- Ruggedized connectors for aircraft systems
- Lightweight solutions that reduce aircraft weight by 15%
- EMI-shielded designs for sensitive equipment
Industrial Automation
- M12 connectors in robotics systems
- Predictive maintenance sensors that reduce downtime by 45%
- High-speed data transmission for factory automation
Renewable Energy
- Waterproof circular interconnects for solar and wind farms
- Connectors that reduce carbon footprint by 15% per unit
- Reliable performance in extreme weather conditions
Medical Equipment
- Hermetically sealed connectors for surgical devices
- Miniature designs that enable minimally invasive procedures
- Sterilizable materials for patient safety
Why Choose YW Connectors?
As a leading electrical connectors manufacturer, YW Connectors delivers:
- Quality: Our gold-plated contacts reduce failure rates by up to 90%
- Innovation: 20% of our connector lineup features IoT-enabled technology
- Value: Though our modern connectors cost more upfront, they last 3x longer
- Customization: We work with you to design the perfect connector solution
- Support: Our engineering team provides technical guidance at every step
Customer Success Story
A major automotive manufacturer was experiencing frequent connector failures in their EV battery systems, costing them thousands in repairs and downtime. After switching to YW’s high-voltage circular connectors:
- Assembly time decreased by 25%
- Connector failure rates dropped by 90%
- They saved $4M annually by reducing replacement frequency
- ROI was achieved in just 18 months
The Future of Circular Connectors
The evolution continues with these emerging trends:
- 5G-ready connectors capable of 10 Gbps data rates
- Sustainable materials reducing environmental impact
- AI-driven predictive maintenance preventing failures before they happen
- Backward-compatible designs that work with legacy systems
Take Action Today
Don’t let outdated connector technology hold your operations back. YW Connectors has the solutions you need to meet today’s demands and prepare for tomorrow’s challenges.
Get in touch with our team to:
- Discuss your specific connector needs
- Request samples of our modern circular connectors
- Get a custom quote for your next project
Visit our website to explore our full range of circular connector solutions and other products: