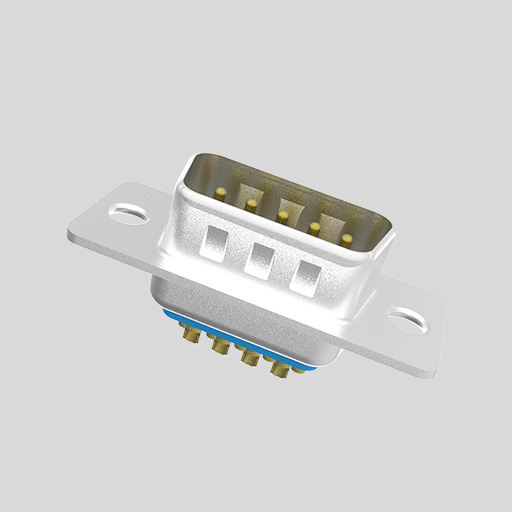
Historia y evolución de los conectores Sub-D
Introducción
Los conectores D-Sub -llamados así por su característica carcasa metálica en forma de D- salieron por primera vez de la cadena de producción de Cannon en 1952, reduciendo al instante el tamaño de las interconexiones multipolo utilizadas en los primeros ordenadores e instrumentos. A lo largo de siete décadas, han pasado de ser curiosidades "en miniatura" a convertirse en una herramienta de uso cotidiano en fábricas, bancos de pruebas, cabinas de aviones e incluso ordenadores de sobremesa.
1. De los mainframes a los microordenadores
Los primeros sub-D ofrecían un apantallamiento fiable y un cierre mecánico seguro en una época en la que la mayoría de los conectores seguían siendo terminales de tornillo. En la década de 1980, cuando la informática pasó de los grandes ordenadores a las máquinas personales, los tamaños compactos de las carcasas (de la A a la E) se adaptaron perfectamente a los recuentos de señales comunes, lo que convirtió a los D-Sub en la E/S externa por defecto para puertos serie, paralelos y de vídeo. Los conocidos tornillos de mariposa garantizaban una conexión a prueba de vibraciones, esencial para la electrónica industrial y militar mucho antes de que existiera el USB.
2. Conteo de Clavijas Estándar y sus Usos de Firma
- 9 patillas (DE-9) - A menudo mal etiquetado como "DB9", este conector se convirtió en sinónimo de puertos serie RS-232 en PC, PLC, máquinas CNC y equipos de red gracias a su reducido tamaño y a su sencillo cableado punto a punto.
- 15 patillas (HD-15/DA-15) - Más conocido como conector VGA, el conector de tres filas de 15 patillas de "alta densidad" transportó vídeo analógico desde el PS/2 de IBM de 1987 hasta la era de las pantallas planas, y todavía está integrado en conmutadores KVM y proyectores. (Subconector D)
- 25 patillas (DB-25) - El puerto paralelo original para impresoras y periféricos SCSI-1; también albergaba RS-232 full-handshake en los primeros módems y routers.
- 37 patillas (DC-37) - Con 19 + 18 contactos, esta carcasa más grande servía para cadenas SCSI multipunto, buses de datos aeroespaciales y mazos de cables de control industrial en los que eran esenciales las conexiones a tierra y los blindajes adicionales.
Estas variantes - "subconectores d de 9 patillas, 15 patillas, 25 patillas y 37 patillas" en muchas búsquedas de catálogos- comparten una geometría de acoplamiento idéntica, lo que permite a los ingenieros mezclar densidades y géneros con capuchones, carcasas traseras y soportes de placa estándar. es.wikipedia.org
3. Robustez: El auge de la d sub conectores estancos
Cuando los armarios de control se trasladaron al exterior, la industria respondió con productos con clasificación IP. d sub conectores estancos. Los subwoofers D IP67 modernos integran juntas tóricas, tornillería inoxidable y carcasas traseras sobremoldeadas para que puedan resistir lavados, niebla salina y ciclos térmicos diarios, sin renunciar a las herramientas ni a las conexiones tradicionales. Los ingenieros conservan el blindaje EMI de la carcasa metálica clásica a la vez que obtienen integridad a prueba de polvo y agua en robots para entornos difíciles, sistemas de tráfico y sensores submarinos.
4. Por qué siguen siendo importantes los conectores D-Sub
- Diseño probado: Décadas de datos de campo significan impedancia, fuerza de retención y resistencia a la vibración predecibles.
- Ecosistema masivo: Millones de piezas crimpadas, soldadas, encajadas a presión e IDC con cualquier tipo de revestimiento y orientación para mantener los costes bajos y las cadenas de suministro resistentes.
- Escalabilidad: Desde el micro-D para satélites hasta el combo-D que transporta potencia + coaxial + fibra, el formato se adapta a los nuevos protocolos sin necesidad de una nueva envoltura mecánica.
- Capacidad de servicio: Los orificios pasantes y los tornillos imperdibles permiten sustituirlos con un destornillador, sin necesidad de aire caliente.
Conclusión
Tanto si necesita subconectores de 9, 15, 25 y 37 pines para una placa antigua como si necesita conectores robustos para una placa nueva. d sub conectores estancos para un quiosco exterior, el humilde D-Sub sigue siendo una opción flexible y preparada para el futuro.
¿Está listo para especificar su próximo conector? Hable hoy mismo con YW Connectors, solicite muestras gratuitas o envíenos sus planos para obtener un presupuesto rápido. ¡Construyamos juntos enlaces fiables!