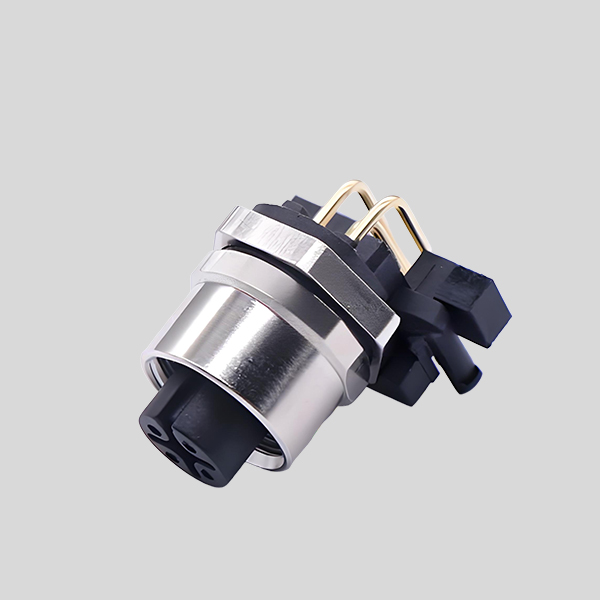
Connecteurs circulaires ou rectangulaires
Which connector is the Right option for You?
L'importance de la géométrie
At first glance, connector choice looks like a simple decision, but geometry drives real‑world performance. Circular connectors seal more evenly around a 360‑degree shell, making them naturals in vibration, wash‑down, or outdoor environments. Rectangular designs stack contacts in rows, so they pack more circuits into less panel area and accept modular inserts for data, power, or pneumatics on the same footprint.
Points forts des connecteurs circulaires étanches
Étanchéité robuste. Les raccords filetés ou à baïonnette, ainsi que les joints toriques, permettent aux connecteurs circulaires de satisfaire aux normes IP67+ avec un minimum d'effort. Un connecteur M12, par exemple, est régulièrement qualifié pour résister à l'humidité et à la poussière dans les ateliers. (Connecteurs d'alimentation M12 ⇒ Parfaits pour les applications industrielles | liant)
Engagement rapide, à l'aveugle.
La coque ronde se centre d'elle-même, ce qui permet aux techniciens de connecter les capteurs par tâtonnement sur les machines encombrées.
Options évolutives de la série M.
- Connecteurs M5 & M8 : ultra-compacts pour les capteurs de proximité et les indicateurs LED où l'espace est restreint mais la fiabilité importante. (Connecteurs d'automatisation M8 pour actionneurs et capteurs - Bulgin)
- Connecteurs M9 et M12 : des outils indispensables pour l'Ethernet industriel, les encodeurs et les câbles de robotique, avec une taille d'équilibrage allant jusqu'à 12 broches.
- Connecteurs M17 et M23 : courant plus élevé (jusqu'à 63 A) pour les servomoteurs, les outils de soudage et les prises d'alimentation des équipements mobiles. (Qu'est-ce que le connecteur M12 ? Types, utilisations et avantages | ATTENDRE)
Comme la coque supporte la charge, les connecteurs circulaires tolèrent davantage de cycles d'accouplement et de chocs que de nombreuses pièces rectangulaires montées sur carte, ce qui prolonge leur durée de vie.
Là où les connecteurs rectangulaires brillent
Densité de contact élevée. Les boîtiers rectangulaires permettent aux concepteurs d'empiler des douzaines, voire des centaines de contacts, tout en conservant la faible profondeur du connecteur, ce qui constitue un avantage pour les plateaux de rack et les armoires de commande. ([PDF] Les connecteurs rectangulaires offrent plus pour moins)
Modularité et médias mixtes. Les systèmes rectangulaires modernes acceptent des blocs encliquetables pour le signal, l'alimentation, la fibre et même l'air comprimé, de sorte qu'un seul boîtier remplace plusieurs entrées de câbles.
Formats traditionnels éprouvés. La famille D-sub classique (DB9, DB25, etc.) est toujours excellente pour les liaisons RS-232/422 et les interfaces série personnalisées. Sa coque métallique offre un blindage EMI intégré et des longueurs de câble qui éclipsent les limites de l'USB. (Connecteurs D-Sub DB9 : Avantages et inconvénients - L-com, Connecteurs D-Sub : Bridging the Connection in Electronics)
Entrée à angle droit et latérale. Les connecteurs rectangulaires s'adaptent facilement aux sorties de câble à 90 degrés, facilitant la décharge de traction à l'intérieur d'ordinateurs de poche minces ou de boîtiers muraux.
Une liste de contrôle pratique pour la sélection
L'environnement : Équipement mobile ou de lavage ? Préférez les modèles circulaires étanches.
Racks de contrôle dans les salles blanches ? La forme rectangulaire permet d'économiser de l'espace sur les panneaux.
Mélange de circuits : Besoin d'une alimentation + d'un signal + de données ? Un système rectangulaire modulaire peut réduire le nombre de pièces.
Vitesse d'installation : Les techniciens de terrain portant des gants préfèrent souvent le filetage à départ unique d'un M12 ou d'un M17 à traction et poussée.
Cycles de maintenance : Les engrenages d'essai à cycle élevé bénéficient de l'usure radiale des contacts circulaires.
Budget et logistique : Les inserts rectangulaires peuvent combiner de nombreuses fonctions, mais si la nomenclature mentionne déjà des surmoulages de la série M, s'en tenir à des inserts circulaires pourrait simplifier l'approvisionnement.
Principaux enseignements
• Circular connectors (M5, M8, M9, M12, M17, M23) waterproof excel in harsh or high‑vibration settings, offering intuitive mating and robust sealing.
- Les connecteurs rectangulaires, y compris les connecteurs D-subs, se distinguent par leur densité de contact, leur souplesse d'utilisation et leur faible encombrement.
- Adaptez la famille de connecteurs aux contraintes mécaniques, aux contraintes d'espace et à la combinaison d'E/S de votre conception, puis standardisez pour rationaliser la maintenance sur l'ensemble de la flotte.
Ready to specify the perfect circular connector waterproof? Contactez l'équipe d'YW dès aujourd'hui pour obtenir des échantillons, des devis rapides et une assistance technique. Mettons votre innovation en relation avec notre portefeuille de 30 000 produits !