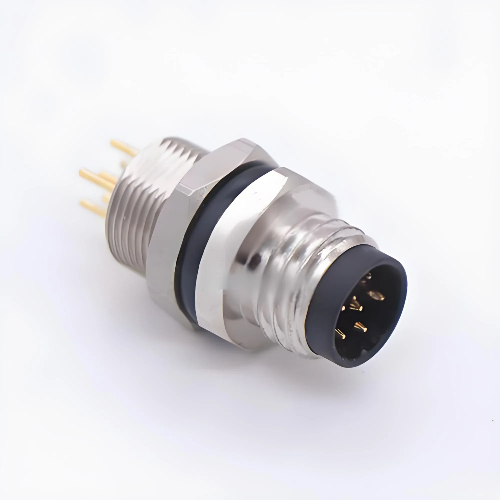
I vantaggi dell'uso dei connettori circolari in ambienti difficili
Introduzione
Nelle applicazioni industriali e tecnologiche, i connettori sono componenti critici per la trasmissione di segnali elettrici ed energia. I connettori standard spesso si guastano in condizioni difficili, mentre i connettori circolari si distinguono in ambienti ostili grazie a prestazioni e durata eccezionali. Questo articolo esplora i vantaggi dei connettori circolari nelle applicazioni più impegnative, che comprendono ambienti ad alta temperatura, elevata umidità e forti vibrazioni.
Struttura e caratteristiche di base dei connettori circolari
I connettori circolari sono generalmente costituiti da spine, tappi, contatti e gusci con un design cilindrico compatto. Rispetto ad altri tipi di connettori, offrono una maggiore resistenza agli urti, alla corrosione e alle prestazioni di tenuta.
Materiale della conca: I materiali comuni della conchiglia includono acciaio inossidabile resistente alla corrosione e lega di alluminio, in modo efficace, condizioni ambientali difficili in modo efficace.
Design di tenuta: Questi connettori sono dotati di robuste capacità di tenuta, che garantiscono l'impermeabilità, l'impermeabilità alla polvere e un'adeguata resistenza alla corrosione.
Resistenza agli urti e agli impatti: Il design strutturale compatto e i materiali ad alta resistenza offrono un'eccellente resistenza alle vibrazioni e agli urti.
Prestazioni in ambienti ad alta temperatura
Le alte temperature possono causare l'invecchiamento del materiale e il cattivo contatto nei connettori standard. I connettori circolari mantengono un funzionamento stabile a temperature estreme grazie al loro design specifico:
Materiali per alte temperature: Utilizzano materiali resistenti al calore, come la poliimmide (PI) e il politetrafluoroetilene (PTFE), che resistono a temperature estreme senza degradare le prestazioni.
Ampio intervallo di temperature operative: I connettori circolari Premium possono funzionare in modo affidabile tra -55°C e +200°C, il che li rende ideali per le applicazioni ad alta temperatura come i vani motore e i macchinari industriali.
Capacità di resistenza alla corrosione
Nelle applicazioni marine, chimiche e del gas, gli ambienti corrosivi mettono a dura prova la stabilità del connettore. I connettori circolari utilizzano gusci resistenti alla corrosione e contatti appositamente trattati per mantenere l'affidabilità:
Contatti placcati in oro: Molti connettori circolari hanno punti di contatto placcati in oro per evitare l'ossidazione e la corrosione, garantendo l'affidabilità della connessione elettrica a lungo termine.
Trattamento anticorrosione della scocca: le scocche costruite in acciaio inossidabile o in lega di alluminio appositamente trattata resistono efficacemente alla corrosione di spruzzi, acidi e alcali.
Protezione avanzata contro l'acqua e la polvere
I connettori circolari raggiungono generalmente il livello di protezione IP67, che consente loro di funzionare normalmente in condizioni di umidità, compresa l'immersione, la pioggia e la neve, pur rimanendo impermeabili alle infiltrazioni di polvere:
Protezione IP67: Questi connettori funzionano efficacemente in ambienti umidi e polverosi, il che li rende adatti alle apparecchiature e ai sistemi di comunicazione esterni.
Design dell'anello di tenuta: Gli anelli di tenuta di alta qualità evitano l'ingresso di umidità e polvere e sono componenti fondamentali per mantenere l'integrità impermeabile e antipolvere.
Resistenza alle vibrazioni e agli urti migliorata
In ambienti soggetti a vibrazioni e impatti elevati, la stabilità del connettore è essenziale. I connettori circolari resistono efficacemente a queste condizioni grazie a:
Design di connessione sicuro: I contatti utilizzano generalmente un design complementare che rimane saldamente collegato in caso di vibrazioni e urti.
Materiali resistenti agli urti: I materiali di rottura e di contatto offrono una forte resistenza agli urti, resistendo agli shock meccanici senza subire danni.
Selezione dei materiali e considerazioni sulla produzione
Conformità alla norma UL94V-0: Molti connettori circolari sono dotati di alloggiamenti in plastica resistente al calore stabilizzati UL94V-0, che garantiscono il mantenimento dell'integrità strutturale in condizioni estreme.
Sistemi di scarico rettilinei: I modelli più avanzati incorporano anelli di scarico della tensione e di blocco con guanti per migliorare la durata e la facilità d'uso nelle applicazioni industriali.
Applicazioni industriali dei connettori circolari
I connettori circolari sono ampiamente utilizzati in diversi settori industriali grazie alla loro affidabilità e durata:
Aerospaziale: utilizzati nei sistemi elettrici, nei satelliti, nei razzi e nelle navicelle degli aerei per mantenere stabile la trasmissione del segnale e la potenza nonostante le variazioni estreme di temperatura, le vibrazioni e gli urti.
Militare: Impiegato in diverse squadre militari per supportare climi estremi e impatti fisici, garantendo la funzionalità delle squadre di comunicazione.
Automobile: sempre più utilizzati nei veicoli elettrici e nei sistemi di guida autonoma, man mano che i requisiti elettrici del settore automobilistico diventano più sofisticati.
Automazione industriale: Garantire connessioni elettriche stabili nelle apparecchiature di automazione, assicurando un funzionamento efficiente della linea di produzione.
Strutture esterne: Le versioni appositamente progettate per la resistenza ai raggi UV sono utilizzate in applicazioni esterne che richiedono un'affidabilità a lungo termine nonostante l'esposizione all'ambiente.
Sviluppi futuri nella tecnologia dei connettori circolari
Con il progredire della tecnologia, il design del connettore circolare continua ad evolversi per soddisfare requisiti sempre più complessi:
Miniaturizzazione: I design più recenti, come i connettori circolari micro-miniaturizzati, combinano prestazioni elevate con dimensioni e peso ridotti, per spazi limitati.
Soluzioni ibride: i moderni connettori circolari incorporano sempre più contatti misti di potenza e di segnale in un unico connettore, semplificando l'installazione e riducendo la complessità del sistema.
Migliori qualifiche ambientali: i produttori continuano a migliorare le capacità di protezione del reddito e alcuni modelli superano ora le classificazioni standard IP67 per le applicazioni in ambienti estremi.
https://www.ywconnectors.com/m12-connectors
Conclusione
I connettori circolari sono diventati soluzioni di connessione indispensabili in ambienti ostili grazie alla loro eccezionale tolleranza alle alte temperature, alla resistenza alla corrosione, all'impermeabilità e alle vibrazioni. Con il progredire della tecnologia, il design e le prestazioni dei connettori circolari continueranno a migliorare per soddisfare requisiti applicativi sempre più complessi ed estremi. Per le industrie che operano in condizioni difficili, i connettori circolari rappresentano una soluzione affidabile e duratura che garantisce l'integrità operativa e riduce potenzialmente i costi di manutenzione e i tempi di fermo del sistema.