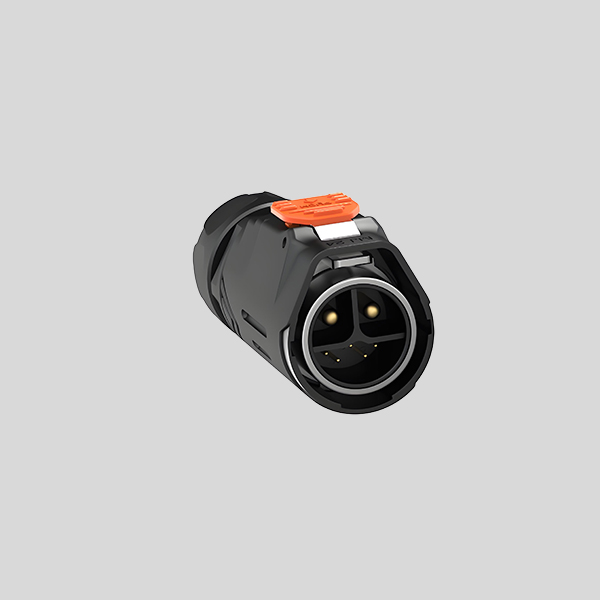
Why Waterproof Circular Connectors Are Crucial for Outdoor Applications
Outdoor electronics are everywhere—smart-city lampposts, solar-panel trackers, autonomous tractors, offshore wind turbines, even Wi-Fi–enabled beach umbrellas. Analysts expect the circular-connector segment alone to double in value from roughly US \$5.3 billion in 2023 to more than US \$10 billion by 2032 as designers race to seal these new devices against the elements.
1. What Makes a Connector “Waterproof” ?
A waterproof circular connector uses two lines of defense. First, an O-ring or molded gland forms a 360-degree seal between plug and receptacle. Second, potting or back-shell gaskets stop capillary action from pulling moisture down the cable jacket. Performance is expressed with the IEC 60529 IP code:
- IP67 = dust-tight and safe after 30 minutes at 1 m depth.
- IP68 = manufacturer-tested for longer or deeper immersion (often 2 m, 24 h).
- IP69K = withstands 80 °C high-pressure wash-downs.
Because circular shells offer continuous geometry, they distribute compression evenly around the seal—one reason circular connectors dominate harsh-environment designs.
2. Environmental Challenges Beyond Water
- Salt fog & chemicals Chlorides in sea spray accelerate galvanic corrosion; fertilizers and road-de-icing salts do the same on land.
- Thermal cycling -40 °C dawns and +85 °C noon sun cause plastics to expand and contract, pumping air (and moisture) past weak seals.
- UV radiation Ultraviolet light embrittles un-stabilized plastics within months.
- Vibration & shock Engines, wind-tower nacelles, and unmanned ground vehicles shake contacts loose if the coupling is not locked.
- Electrical noise High-speed data lines need 360-degree shielding or differential-pair layouts to meet EMC regulations.
Marine-safety body ABYC flags corrosion as the root cause of 97 % of on-board electrical failures—most beginning at the connector.
3. Key Features to Look For in Waterproof Circular Connectors
Feature | Why It Matters in the Field |
---|---|
Ingress rating ≥ IP67 | Survives rain, wash-downs, temporary immersion |
Corrosion-resistant shells | Nylon, nickel-plated brass, or stainless steel outlast bare zinc alloys |
Positive-lock coupling | Threaded or bayonet systems stop accidental decoupling under vibration |
Wide temperature range | -40 °C to +105 °C supports desert, arctic, and engine-bay installs |
High mating cycles | Gold-plated contacts rated 3 000+ insertions prevent downtime in rental gear |
EMI shielding | 360-degree backshells or twisted-pair inserts protect high-speed comms |
4. Real-World Application Snapshots
- LED Street Lighting City planners prefer pre-molded, IP68 waterproof connector solutions so crews can “plug-and-play” luminaires from bucket trucks without opening junction boxes.
- Solar PV Arrays Tracking actuators and string combiners sit inches above gravel, where blown dust and rain mix into a conductive slurry. Sealed circular connectors keep DC arcs in check.
- Agricultural Drones Folding arms must be removed for transport; bayonet-style IP67 power/data connectors let operators swap arms in seconds while keeping pesticide mist out.
- Electric-Vehicle Chargers Level-2 curb-side pedestals endure snow-melt salts. Nickel-plated brass shells and molded cable glands deliver 10-year service life.
- Deck Gear on Workboats Hydraulic-winch sensors see continuous spray. ABYC-compliant IP68 connectors eliminate the need for expensive hermetic feed-throughs.
These examples highlight why designers are moving away from hobby-grade grommets toward purpose-built waterproof circular connectors.
5.Best Practices for Installation & Maintenance
- Torque matters. Hand-tighten threaded couplings, then add a quarter-turn with calibrated pliers if the datasheet specifies. Over-tightening can crush O-rings; under-tightening breaks the seal.
- Use dielectric grease sparingly on the mating face; it displaces micro-films of water and eases future unmating.
- Support the cable. A drip-loop below the connector lets gravity pull water away instead of into the shell.
- Inspect annually. Look for discoloration, green patina (copper oxide), or cracked boots—early warnings that a seal has failed.
- Test with pressure or megger. A 500 V insulation-resistance check or simple submersion bubble test finds pin-hole leaks before they become service calls.
Follow these steps and a quality connector should meet or exceed its published IP rating throughout the product’s lifespan.
6. Future Trends—Smaller, Faster, Smarter
- Miniaturization 12 mm-diameter shells now carry USB 3.2 or 10 Gb Ethernet thanks to precision die-cast shielding and low-skew pin layouts.
- Hybrid power-data inserts A single connector can deliver 60 W USB-PD plus 5 A auxiliary power—simplifying robotic joints.
- Additive-manufactured backshells 3-D printed lattice structures cut weight in UAVs while channeling potting resin more efficiently.
- Condition monitoring Embedded temperature or moisture microsensors inside the connector report seal health over Bluetooth for predictive maintenance.
These advances reinforce the central point: as edge devices get smarter, so must the humble connector that keeps them alive.
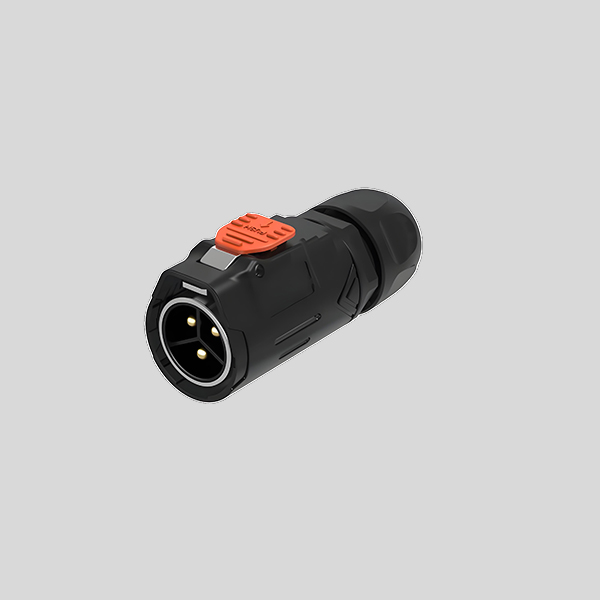
7. YW Precision Electronics: A Ready-Made Waterproof Connector Solution
The YW MY24 series embodies many of the best practices outlined above. Originally developed for shipboard lighting, it features:
- IP67 sealing verified to 2 m for 48 h
- Quick lock solution that mates in < 3 s
- Bear outdoor harsh environment
- Up to 50 A at 300 V
- Cable-to-cable, cable-to-panel, and PCB-mount variants for design flexibility
Founded in 2013, YW Precision Electronics manufactures various circular connectors per year under ISO 9001 controls and backs every shipment with 24-hour technical support. From prototype loom to mass-produced harness, YW provides a one-stop, cost-effective path to ruggedized connectivity.
8. Checklist for Selecting Your Next Connector
- Define exposure level. Splashing? Jet-wash? Full submersion? Match the IP code accordingly.
- Confirm material compatibility. Nylon for weight, brass for shielding, stainless for extreme corrosion.
- Align electrical specs. Voltage, current, surge rating, and any data-rate requirements.
- Plan for field service. Choose crimp inserts if technicians must re-terminate on site; over-molded pigtails if they won’t.
- Verify compliance. Look for UL, CE, ABYC, or MIL-DTL documentation when regulations apply.
- Evaluate vendor support. Rapid sampling, CAD models, and customized over-molds lower total development time.
9. Conclusion
Whether you are illuminating a pedestrian plaza, steering an autonomous tractor, or wiring deck lights on a patrol boat, waterproof circular connectors are your gear’s first—and often only—line of defense against moisture, salt, and mechanical abuse. By understanding IP ratings, real-world hazards, and the feature set that defines a robust solution, you can choose connectors that keep power and data flowing long after lesser parts have failed. YW Precision Electronics’ SP series shows how modern waterproof connector solutions combine speed of installation with decade-long reliability, allowing engineers to innovate outdoors with confidence.